A few elements like carbon, sulphur, gold, platinum, copper, silver, mercury and noble gases, occur in the free state while others in combined forms like oxides, sulphides, carbonates, sulphates, silicates etc. in the earth’s crust. Metallurgy is a branch of chemistry that deals with the processes that are used for the extraction of metals in their pure form.
Among metals, aluminium is the most abundant. It is the third most abundant element in earth’s crust (8.3% approx. by weight). It is a major component of many igneous minerals including mica and clays. Many gemstones are impure forms of Al2O3 and the impurities range from Cr (in ‘ruby’) to Co (in ‘sapphire’). Iron is the second most abundant metal in the earth’s crust. It forms a variety of compounds and their various uses make it a very important element. The principal ores of aluminium, iron, copper, magnesium, and zinc have been given in the following table
Sr.No. | Metal | Minerals | Ore |
1 | Iron (Fe) | Haematite (Fe2O3) Magnetite (Fe3O4) Limonite (2Fe2O3.3H2O) Iron pyrite (FeS2) Siderite (Fe2CO3) | Haematite (Fe2O3) |
2 | Copper (Cu) | Copper pyrite (CuFeS2) Malachite (CuCO3.Cu(OH) 2) Cuprite (Cu2O) Copper Glance (Cu2S) | Copper glance (Cu2S) |
3 | Zinc (Zn) | Zinc blende (ZnS) Zincite (ZnO) Calamaine ZnCO3 | Zinc blende (ZnS) |
4 | Magnesium (Mg) | Magnasite (MgCO3) Dolomite (MgCO3.CaCO3) Epsum salt (MgSO4.7H2O) | Dolomite (MgCO3, CaCO3) |
5 | Aluminium (Al) | Bauxite (Al2O3.2H2O) Cryolite Na3AlF6 China clay (Al2O3.2SiO2.2H2O) | Bauxite (Al2O3.2H2O) |
Terminology Used in Metallurgy:
Metallurgy:
The scientific and technological process used for the isolation of the pure metal from its ores is known as metallurgy.
Depending upon the nature of metal and the nature of ore, different methods are used in the extraction process. The different metals used are a) Pyrometallurgy, b) Hydrometallurgy and c) Electrometallurgy
- Pyrometallurgy: A process in which the ore is reduced to metal at high temperature using a suitable reducing agent like carbon, hydrogen, aluminium, etc. is called pyrometallurgy.
- Hydrometallurgy: A process of extraction of metals from aqueous solutions of their salts using suitable reducing agents is called hydrometallurgy.
- Electrometallurgy: A process of extraction of metals by electrolytic reduction of molten (fused) metallic compounds is called electrometallurgy.
Minerals:
A naturally occurring chemical substance obtained in mining which contains the metal in a free state or combined state is called mineral.
Ores:
A mineral containing a high percentage of metal from which the metal can be profitably extracted is called an ore. Ex: Copper glance (Cu2S), Haematite ( Fe2O3). Ores may be divided into four groups
- Native Ores: These ores contain the metal in free state eg. Silver gold etc.
- Oxidized Ores: These ores consist of oxides or oxy-salts (eg. carbonates, phosphate) and silicate of metal. e.g. Haematite, the ore of iron Fe2O3, Bauxite the ore of aluminium Al2O3.2H2O, Cassiterite SnO2, Cuprite Cu2O, Zincite ZnO, Ilmenite FeTiO3, Rutile, TiO2 etc.
- Important carbonate ores are limestone (CaCO3), Calamine (ZnCO3), Siferite, (FeCO3), Cerrusite, (PbCO3) etc.
- Important sulphate ore is Anglesite (PbSO4).
- Sulphurised Ores: These ores consist of sulphides of metals like iron, lead, mercury etc. e.g. iron pyrites (FeS2). galena (PbS), Cinnabar (HgS). They are also called pyrites
- Halide ores: Metallic halides are very few in nature. Chlorides are most common examples include horn silver (AgCl) carnallite KCl. MgCl2.6H2O and fluorspar (CaF2), Cryolite, (Na3AlF6).
- Silicate Ores: Hemimorphite, (2ZnO.SiO2.H2O)
Gangue:
ores are usually contaminated with unwanted earthly(sandy) or undersides materials known as gangue. For example in the extraction of iron, silica is gangue present in haematite (Fe2O3).
Mineral Wealth in India:
Metal | Reserves | States |
Iron | Approx. 1750 crore tonnes | Goa, Madhya Pradesh, Bihar, Karnataka, Orissa and Maharashtra. |
Aluminium | 2 million tonnes. | Bihar, Goa, Madhya Pradesh, Maharashtra, Tamil Nadu, Gujarat, Karnataka, Orissa, Uttar Pradesh, Andhra Pradesh, Jammu & Kashmir and Rajasthan. |
Copper | 60 crore tonnes | Singhbum district (Bihar), Balaghat district (Madhya Pradesh) and Jhunjhunu district (Rajasthan) |
Zinc and Lead | Not significant | Zawar mines near Udaipur (Rajasthan) and at Hazaribagh (Jharkhand), Sargipalli mines in Orissa and Bandalamottu lead project in Andhra Pradesh, Gujarat and Sikkim |
Tin | – | Hazaribagh (Jharkhand) and Orissa |
Gold and Silver | – | Gold from Kolar fields and Hutti gold fields (Karnataka). lead-zinc ores of Zawar mines (Rajasthan) contain some silver |
Titanium | 100 to 150 million tonnes | beach sands of Kerala and Tamil Nadu |
Sodium | Ladakh and Kashmir and sea water |
Steps Involved in the Extraction of Metals:
The extraction and isolation of metals from ores involve the following major steps:
- Concentration of the ore (or) Purification of the Ore
- Conversion of ores into oxides or other desired compounds.
- Reduction of ores to form crude metals
- Refining of metals
Step – 1: The concentration of the ore:
The removal of earthy and siliceous impurities (i.e. gangue or matrix) from the ores is called concentration, dressing or benefaction. of ores. This process increases the percentage of the desired metal or metal compound in the ore.
It involves several steps and selection of these steps depends upon the differences in physical properties of the compound of the metal present and that of the gangue. The type of the metal, the available facilities and the environmental factors are also taken into consideration.
Hand-picking:
In this process the earthy impurities (heavy impurities) which are present in the ore like rocky materials, pellets are picked by hand.
Pulverizing:
Ore obtained from mines is in a lump form. It is finely ground to form powdered ore, the process is called pulverizing.
For pulverizing the ore, jaw crushers or grinders are used. The big lumps of the ore are brought in between the plates of a crusher forming a jaw. One of the plates of the crusher is stationary while the other moves to and fro and the crushed pieces are collected below.
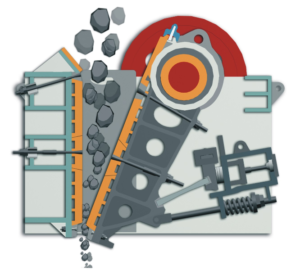
The crushed pieces of the ore are then pulverized (powdered) in a stamp mill. The heavy stamp rises and falls on a hard die to powder the ore.
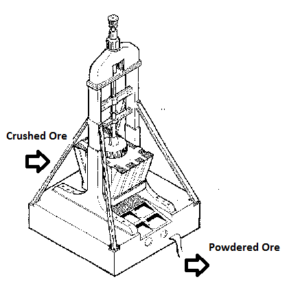
Hydraulic washing or Gravity Separation:
It is done by two ways a) Wilfley table method and b) Hydraulic classifier method
- Wilfley Table Method: The pulverized ore is made to fall through the hopper on the slanting floor of Wilfley’s table. The floor of Wilfley’s table is made up of fixed wooden triangular strips called cleats or riffles. This floor is continuously vibrating. A running stream of water is passed across the table. The lighter gangue particles are washed away and the heavier ore particles settle between wooden cleats of the table.
- Hydraulic Classifier Method: Hydraulic classifier consists of a tank having a hopper at the top and a pipe for carrying pressurized water. The ore is fed into the tank from the top, and the water is allowed with high pressure from the bottom of the tank. During this process the lighter impurities which are adhered to the ore float over the water which is removed by flowing water. The ore particles will settle down at the bottom of the tank. In this process, the lighter impurities are removed.
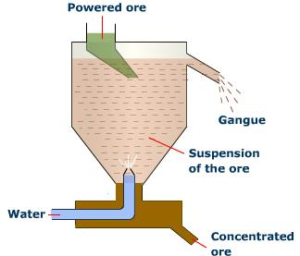
Magnetic separation:
In this method, electromagnetic separators are used. This method of concentration is used when either the ore or impurities associated with it are magnetic in nature.
This process is used for the Iron ore only. → The ore is passed through a belt which is connected by two rotating wheels, one among is made up of magnetic material. Once the ore is passed through the belt, the ore or impurity particles having magnetic properties are attracted to the magnetic wheel and fall near to it. While the impurities or ore particles which are nonmagnetic are not attracted by the magnetic wheel and fall away from the magnetic wheel as shown in the figure. Thus two separate heaps are formed.

Example: Cassiterite is ore of tin (Sn) contains non-magnetic stannic oxide SnO2, the magnetic impurity tungstate or wolframite FeWO4. They can be separated by this method.
Froth floatation:
Principle: The surface of sulphide ores is preferentially wetted by oils while that of gangue is preferentially wetted by water. Hence this method is used for concentration of sulphide ores.
Process: In this process, a suspension of the powdered ore is made with water. Certain oils like pine oil, eucalyptus oil, xanthates or fatty acids are added as collectors along with froth stabilisers. Collectors are the chemical substances which enhance non-wettability of the mineral particles. Froth stabilizers are the chemical substances stabilise the froth. e.g.: cresols, aniline.
A rotating paddle agitates the mixture and draws air in it. As a result, a froth is formed which carries the mineral particles. The froth is light and is skimmed off. It is then dried for recovery of the ore particles

Depressants are the chemical substances which help to separate two sulphide ores by adjusting the proportion of oil to water. For e.g., in case of an ore containing ZnS and PbS, the depressant used is NaCN. It selectively prevents ZnS from coming to the froth but allows PbS to come with the froth.
Leaching:
Leaching is a process in which powdered ore is treated with a suitable reagent which is selectively dissolved the ore but not the impurities. This process is often used if the ore is soluble in some suitable solvent. It is a chemical method used for purification of ore.
Leaching of Alumina from Bauxite:
The principal ore of aluminium bauxite consists of three chemical impurities ferric oxide (Fe2O3), silica (SiO2) and titanium oxide (TiO2).
Bayer’s Process:
This method is used when major impurity is ferric oxide (Fe2O3)
The ore is treated with Sodium hydroxide solution (NaOH), at about 423 K. The impurity ferric oxide (Fe2O3) does not react with NaOH and can be removed by filtration.
Al2O3.2 H2O(s) + 2NaOH(aq) → 2NaAlO2 (aq) + 3 H2O(l)
The solution is filtered to remove insoluble impurities and is agitated with freshly prepared Al(OH)3, so that the aluminium in NaAlO2 get precipitated to Al(OH) 3.
2NaAlO2 + 2 H2O → NaOH + Al(OH) 3
The precipitate obtained in the process is washed, dried and heated to get Al2O3.
Al(OH3 →Heat Al2O3 + 3 H2O
Hall’s Process:
In this process, the ore and sodium carbonate are fused together to convert aluminium oxide into soluble sodium meta aluminate.
Al2O3.2 H2O(s) + Na2CO3(aq) → 2NaAlO2 (aq) + CO2(g) + 2H2O(l)
The insoluble residue contains the impurities of silica and iron oxide. The filtrate is warmed and neutralized by passing carbon dioxide through the solution to produce aluminium hydroxide.
2NaAlO2 + 3 H2O + CO2(g) → 2Al(OH) 3 + Al(OH)3 + Na2CO3(aq)
The precipitate obtained in the process is washed, dried and heated to get Al2O3.
Al(OH3 →Heat Al2O3 + 3 H2O
Leaching of Silver and Gold:
In the metallurgy of silver and that of gold, the respective metal is leached with a dilute solution of NaCN or KCN in the presence of air (for O2) from which the metal is obtained later by replacement:
4M(s) + 8CN– (aq) + 2H2O + O2(g) → 4[M(CN) 2] – (aq) + 4OH–(aq) (M= Ag or Au)
2[M (CN) 2] – (aq) + Zn(s) → [Zn(CN)4] – – (aq) + 2 M(s)
Step – 2: Extraction of Crude Metal from Concentrated Ore:
The concentrated ore must be converted into a form which is suitable for reduction. Usually, the sulphide ore is converted to oxide before reduction. Oxides are easier to reduce. Thus isolation of metals from concentrated ore involves two major steps viz., (a) conversion to oxide, and (b) reduction of the oxide to metal.
Roasting:
Roasting is a process in which ores are heated to a high temperature below their melting point in the presence of an excess of air.
Calcination is generally used for ores containing carbonates and hydrated oxides.
Roasting is carried out in a reverberatory furnace This process is usually used for sulphide ores. During this process the moisture is removed, organic matter is destroyed and non-metallic impurities like that of S, P and As are oxidized and removed as volatile gases.
S8 + 😯2 → 8SO2↑ (Sulphur dioxide)
P4 + 5O2 → 2P2O5 ↑ (Phosphorus pentaoxide)
4As + 3O2 → 2As2O3↑ (Arsenious oxide)
Ores are generally converted into metallic oxides
2ZnS (Zinc sulphide) + 3O2 → 2ZnO (Zinc oxide) + 2SO2↑
2PbS (Lead oxide) + 3O2 → 2PbO (Lead oxide) + 2SO2↑
2Cu2S (Cuprous sulphide) + 3O2 → 2Cu2O (Cuprous oxide) + 2SO2↑
Calcination:
Calcination is a process in which the ore is heated to a high temperature below its melting point in the absence of air or in a limited supply of air.
It is carried out in a reverberatory furnace In this process moisture, volatile impurities like carbon dioxide, sulphur dioxide are expelled from the ore. The ore is made porous. Carbonate ores decompose to form a metal oxide and carbon dioxide.
ZnCO3 + Heat →ZnO(s) + CO2(g) ↑
CaCO3 + Heat →CaO(s) + CO2(g) ↑
CaCO3.MgCO3 + Heat →CaO(s) + MgO(s) + 2CO2(g) ↑
2Fe2O3 . 3H2O + Heat →2Fe2O3 + 3H2O(g) ↑