Science > Physics > Thermal Properties of Matter and Thermodynamics > Measurement of Temperature
LIST OF SUB-TOPICS:
- Introduction
- Thermometer
- Mercury Thermometer
- Constant Volume Gas Thermometer (CVGT)
- Constant Pressure Gas Thermometer (CPGT)
- Platinum Resistance Thermometer (PRT)
- Thermocouple
- Pyrometer
- Thermistors
- Liquid Crystal Thermometer
In last article, we have studied different temperature scales. In this article, we shall discuss methods of measurement of temperature and thermometers.
Temperature can be defined in several ways:
- The temperature may be defined as the degree of hotness or coldness of a body.
- The temperature of a body is an indicator of the average thermal energy (Kinetic energy) of the molecules of the body.
- It is that physical quantity which decides the flow of heat in bodies brought in contact. Heat always flow from the body at higher temperature to the body at the lower temperature.
It is measured in °C (centigrade or Celsius) or K (Kelvin). It is measured by a device called a thermometer. The common thermometer is a mercury thermometer.
The branch of Physics that deals with the measurement of temperature is called Thermometry.
Thermometer:
A thermometer is an instrument used to measure temperature. It works based on the principle that certain physical properties of materials change with temperature. Thermometers typically contain a temperature-sensitive element, such as mercury, alcohol, or a thermocouple, which expands or contracts in response to temperature changes. Thermometers are widely used in various fields, including meteorology, medicine, food processing, and industrial processes, to monitor and control temperature.
Temperature is often measured with the use of a thermometer. To understand how thermometers work, one must first understand the concept of thermal equilibrium. Two bodies are said to be in thermal equilibrium with each other if no transfer of heat takes place when they are brought in contact, clearly, the two bodies are at the same temperature.
Mercury Thermometer:
A Mercury thermometer is a type of thermometer that uses mercury as the temperature-sensitive element. Mercury thermometer work on the principle of thermal expansion of liquids. In case of mercury thermometer, mercury (liquid) expands when the temperature increases. This rise in the level of mercury in the capillary gives the temperature readings.
Elements of Mercury Thermometer:
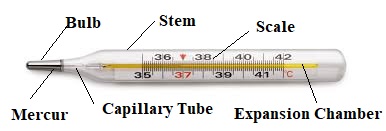
- Mercury as the Temperature-Sensitive Element: In a mercury thermometer, the temperature-sensitive element is a column of mercury contained within a glass capillary tube. Mercury is a suitable choice for thermometers because it expands and contracts in a uniform manner with changes in temperature and it does not stick to the glass.
- Glass Capillary Tube: The thermometer consists of a sealed glass tube with a small bulb at one end and a narrow capillary tube. The capillary tube contains the mercury column, and the bulb serves as a reservoir for the mercury.
Working of Mercury Thermometer:
As the temperature increases, the mercury inside the thermometer expands and rises up the capillary tube. Conversely, when the temperature decreases, the mercury contracts and retreats back into the bulb.
Calibration:
Mercury thermometers are calibrated to provide accurate temperature readings. The glass tube is marked with a scale that correlates the height of the mercury column with specific temperature values. The scale is often marked in Celsius (°C) or Fahrenheit (°F) degrees.
Advantages of Mercury Thermometer:
Mercury thermometers have been widely used for temperature measurement in various fields for several reasons, which include the following advantages:
- Accuracy: Mercury thermometers provide accurate temperature readings over a wide range of temperatures. Mercury expands and contracts uniformly with changes in temperature, allowing for precise measurement.
- Wide Range: Mercury thermometers cover a wide temperature range from −37 to 356 °C (−35 to 673 °F); the instrument’s upper temperature range may be extended through the introduction of an inert gas such as nitrogen.
- Thermal Conductivity: Mercury has a high thermal conductivity, meaning it responds quickly to changes in temperature. This characteristic enables mercury thermometers to provide relatively fast temperature readings compared to some other types of thermometers.
- Versatility: Mercury thermometers can measure temperatures across a broad range, making them suitable for various applications in laboratories, medical settings, and industrial environments.
- Linear Expansion: Mercury expands and contracts in a linear manner with changes in temperature, making it relatively easy to calibrate mercury thermometers for accurate temperature measurement.
- Ease of Reading: Mercury is opaque and shining. It does not stick to glass-sides. The clear glass tube and mercury column make it easy to read the temperature on a mercury thermometer. The markings on the scale are visible and straightforward to interpret.
- Longevity: When handled properly, mercury thermometers can last a long time without significant degradation in accuracy or performance.
Disadvantages of Mercury Thermometer:
While mercury thermometers are accurate and reliable, they pose potential health and environmental hazards due to the toxicity of mercury. Accidental breakage of a mercury thermometer can release mercury vapour, which is harmful if inhaled. For this reason, many countries have phased out the use of mercury thermometers in favour of safer alternatives, such as digital thermometers or alcohol-filled thermometers.
Despite safety concerns, mercury thermometers have been widely used and have played a significant role in temperature measurement in various fields. However, their use is decreasing due to environmental and health considerations, and alternative thermometer technologies are becoming more prevalent.
Constant Volume Gas Thermometer:
A Constant Volume Gas Thermometer (CVGT), is a device used to measure temperature based on the principles of ideal gas behaviour. CVGT work on principle of Gay-Lussac’s law. Gay- Lussac’s Law states that when volume of a gas is constant, the pressure of the gas is directly proportional to its absolute temperature. As the temperature changes, the pressure changes accordingly. Measuring the pressure, temperature can be measured.
Constant volume gas thermometers are used primarily in scientific research and metrology (the science of measurement) for precise temperature measurements. They are often employed in situations where high accuracy and precision are required, such as in fundamental scientific experiments and calibration laboratories.
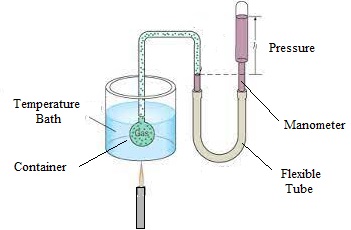
Construction:
The components of the apparatus are as follows:
- Container: The CVGT consists of a container with a fixed volume. This container is typically made of a material that does not react with the gas being used and can withstand high pressures and temperature changes.
- Gas: The container is filled with a gas, often a noble gas like helium or argon, at a known pressure and temperature. The gas is chosen for its inert properties and its ability to follow the ideal gas law accurately over a wide range of temperatures and pressures.
- Pressure Measurement System: A pressure measurement system is integrated into the CVGT to measure the pressure of the gas inside the container. This system may include a manometer, Bourdon gauge, or other pressure sensing devices capable of accurately measuring the pressure of the gas.
- Thermometer: A thermometer is used to measure the temperature of the gas inside the container. This thermometer may be a separate device inserted into the container or integrated directly into the CVGT.
- Sealing Mechanism: The container of the CVGT must be tightly sealed to prevent gas leaks and maintain a constant volume. The sealing mechanism may involve O-rings, gaskets, or other sealing materials capable of withstanding high pressures and temperature changes.
- Supporting Components: Various supporting components such as valves, fittings, and pressure regulators may be included in the construction of the CVGT to facilitate gas handling, pressure control, and temperature measurement.
- Calibration: The CVGT is calibrated by measuring the pressure of the gas at two known temperature points, typically at the freezing and boiling points of water under standard atmospheric pressure. These temperature-pressure data points are then used to establish a temperature-pressure relationship for the gas.
Measurement of Temperature:
Once calibrated, the CVGT can be used to measure temperatures by measuring the pressure of the gas at the temperature of interest and using the established temperature-pressure relationship to determine the corresponding temperature.
By Gay Lussac’s Law at constant volume of a gas
P α T
Thus
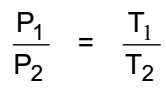
Where, P1 = Initial Pressure (Known)
T1 = Initial Absolute Temperature (Known)
P2 = Final Pressure (To be measured)
T2 = Final Absolute Temperature (To be calculated)
Advantages of CVGT:
CVGTs offer several advantages in temperature measurement, especially in situations where high accuracy and precision are required. Here are some of the key advantages:
- High Accuracy: CVGTs provide highly accurate temperature measurements. They operate based on the ideal gas law, which establishes a direct relationship between the pressure of the gas and the absolute temperature. This relationship allows for precise temperature determination.
- Wide Temperature Range: CVGTs can measure temperatures across a wide range, from cryogenic temperatures to very high temperatures. This versatility makes them suitable for various applications in scientific research, metrology, and industrial processes.
- Direct Measurement: CVGTs directly measure the temperature of the gas by measuring its pressure at constant volume. This direct measurement approach eliminates the need for complex conversions or corrections, leading to more straightforward and accurate temperature readings.
- Insensitive to Gas Composition: CVGTs are relatively insensitive to the composition of the gas used inside the thermometer. As long as the gas behaves ideally, its composition does not significantly affect temperature measurements, enhancing the reliability and universality of CVGTs.
- Stable Calibration: Once calibrated, CVGTs maintain stable and consistent temperature-pressure relationships over time. This stability allows for long-term use without frequent recalibration, reducing maintenance requirements and ensuring reliable temperature measurements.
- High Precision: CVGTs can achieve high precision in temperature measurement, especially when using sensitive pressure measurement devices. This precision is essential in scientific research, quality control, and other applications where precise temperature control is critical.
- Minimal Thermal Lag: CVGTs typically exhibit minimal thermal lag, meaning they respond quickly to temperature changes. This rapid response time is advantageous in dynamic temperature measurement applications and experiments requiring real-time temperature monitoring.
- Suitability for Fundamental Studies: CVGTs are often used in fundamental scientific studies and metrological applications where precise temperature measurement is essential. They provide a basis for establishing temperature scales and calibrating other temperature measurement devices.
Disadvantages of CVGT:
While Constant Volume Gas Thermometers (CVGTs) offer many advantages, they also have some notable disadvantages and limitations:
- Complexity: CVGTs can be relatively complex to construct and operate compared to simpler temperature measurement devices like liquid-in-glass thermometers or electronic thermometers. They require precise calibration and careful handling to ensure accurate temperature measurements.
- Specialized Equipment: The construction and calibration of CVGTs often require specialized equipment and expertise, making them less accessible and practical for everyday temperature measurement tasks.
- Pressure Sensitivity: CVGTs are highly sensitive to changes in pressure, which can affect the accuracy of temperature measurements. Variations in ambient pressure or pressure within the gas chamber can introduce errors in temperature readings.
- Limited Practicality: While CVGTs offer high accuracy and precision, they may not always be the most practical choice for temperature measurement in certain applications. They are typically used in laboratory settings or metrology applications where precise temperature control is required.
- Safety Concerns: Some gases used in CVGTs, such as helium or argon, can pose safety risks if mishandled or released into the environment. Additionally, the high pressures involved in CVGTs can present safety hazards if proper precautions are not taken.
- Inertia and Response Time: CVGTs may exhibit inertia and response time delays, especially when compared to more modern temperature measurement devices like electronic thermometers. This slower response time can be a limitation in applications requiring rapid temperature changes.
- Environmental Impact: The use of certain gases in CVGTs, particularly if they are released into the environment, can have environmental implications. Gases such as helium and argon are finite resources, and their extraction and use contribute to environmental impacts.
- Cost: CVGTs can be costly to manufacture, calibrate, and maintain, particularly when compared to other types of thermometers. The specialized equipment and expertise required for CVGTs can contribute to higher costs associated with their use.
While CVGTs remain important tools for precise temperature measurement in certain applications, it’s essential to consider their limitations and weigh them against the specific requirements of the measurement task at hand. In many cases, alternative temperature measurement methods may offer a more practical and cost-effective solution.
Constant Pressure Gas Thermometer:
A Constant Pressure Gas Thermometer (CPGT), is a device used to measure temperature based on the principles of ideal gas behaviour. CPGT work on principle of Charle’s law. Charle’s Law states that when pressure of a gas is constant, the volume of the gas is directly proportional to its absolute temperature. As the temperature changes, the volume changes accordingly. Measuring the volume, temperature can be measured.
Construction:

The thermometric part consists of a silica bulb A (thermometer Bulb) connected to exactly similar bulb R through capillary tube ab. Bulb R is filled with mercury, this mercury can be drained out by operating draining knob at the bottom of bulb R.
The compensating part consists of another bulb B exactly similar bulbs A and R is connected to the system using capillary tube cd exactly similar to capillary tube ab (same length and same bore). The two capillary tubes ab and cd are always kept side by side to remain at the same temperature.
The thermometric part and the compensating part are connected to each other through manometer M.
Working:
All the three bulbs A, R, and B are kept in melting ice and ends of capillary tube are opened so that all parts of system are at atmospheric pressure. Bulb R is filled with mercury and the ends of capillary tubes are sealed and system is made air tight.
Bulb A is immersed in a bath of unknown temperature, while bulbs R and B are still maintained in melting ice. The pressure of air in bulb A increases thus there is difference in the level of mercury in the manometer M. The mercury in Bulb R is drained out by operating draining knob till the level in arms of manometer is equal again. The volume of drained mercury is measured.
Calculation
Θ = vTo/(V-v)
Where Θ = Temperature to be measured
To = Temperature of air in bulbs B and R
v = Volume of mercury taken out
V = Volume of air in each capillary tube ab and cd
Advantages of CPGT:
Constant Pressure Gas Thermometers (CPGTs) offer several advantages in temperature measurement, particularly in situations where high accuracy and stability are required. Here are some of the key advantages of CPGTs:
- High Accuracy: CPGTs provide highly accurate temperature measurements. They operate based on the principle of constant pressure gas behaviour, which allows for precise determination of temperature based on the volume of the gas.
- Stability: CPGTs maintain stable temperature-volume relationships over time. Once calibrated, they exhibit consistent and predictable responses to changes in temperature, making them reliable instruments for temperature measurement.
- Direct Measurement: CPGTs directly measure temperature based on the volume of the gas at constant pressure. This direct measurement approach eliminates the need for complex conversions or corrections, leading to more straightforward and accurate temperature readings.
- Wide Temperature Range: CPGTs can measure temperatures across a wide range, from cryogenic temperatures to very high temperatures. This versatility makes them suitable for various applications in scientific research, metrology, and industrial processes.
- Insensitivity to Gas Composition: CPGTs are relatively insensitive to the composition of the gas used inside the thermometer. As long as the gas behaves ideally, its composition does not significantly affect temperature measurements, enhancing the reliability and universality of CPGTs.
- Minimal Thermal Lag: CPGTs typically exhibit minimal thermal lag, meaning they respond quickly to temperature changes. This rapid response time is advantageous in applications requiring real-time temperature monitoring and control.
- Practicality in Controlled Environments: CPGTs are well-suited for use in controlled laboratory environments where precise temperature control is required. They offer high accuracy and stability under controlled conditions, making them valuable tools for scientific research and experimentation.
- Long-Term Stability: Once calibrated, CPGTs maintain stable temperature-volume relationships over extended periods. This long-term stability allows for continuous and reliable temperature measurement without the need for frequent recalibration.
Disadvantages of CPGT:
Constant Pressure Gas Thermometers (CPGTs) have several disadvantages and limitations despite their accuracy and stability. Some of the main disadvantages include:
- Complexity and Cost: CPGTs can be complex and expensive to construct, calibrate, and maintain. They require precise engineering and calibration procedures, as well as specialized equipment and expertise, which can increase their cost and complexity compared to other types of thermometers.
- Pressure Sensitivity: CPGTs are highly sensitive to changes in pressure, which can affect the accuracy of temperature measurements. Variations in ambient pressure or pressure within the gas chamber can introduce errors in temperature readings, requiring careful pressure control and compensation.
- Limited Practicality: While CPGTs offer high accuracy and stability, they may not always be the most practical choice for temperature measurement in certain applications. They are typically used in laboratory settings or metrology applications where precise temperature control is required, but they may not be suitable for field or industrial applications due to their complexity and cost.
- Susceptibility to Contamination: CPGTs are susceptible to contamination of the gas chamber, which can affect the accuracy and stability of temperature measurements. Contaminants such as moisture, gases, or particulate matter can introduce errors and require thorough cleaning and maintenance procedures.
- Limited Range of Gas: CPGTs are typically designed to operate with specific gases that behave ideally over a wide range of temperatures and pressures. The choice of gas can limit the temperature range and applicability of CPGTs in certain situations.
- Safety Concerns: The use of certain gases in CPGTs, such as helium or argon, can pose safety risks if mishandled or released into the environment. Additionally, the high pressures involved in CPGTs can present safety hazards if proper precautions are not taken. The vapours of mercury used is poisonous.
- Response Time: CPGTs may exhibit slower response times compared to other types of thermometers, especially in situations where rapid temperature changes occur. This slower response time can be a limitation in applications requiring real-time temperature monitoring and control.
Despite these disadvantages, CPGTs remain valuable tools for precise temperature measurement in controlled laboratory environments and metrology applications where accuracy and stability are paramount. However, it’s essential to consider their limitations and weigh them against the specific requirements of the measurement task at hand. In many cases, alternative temperature measurement methods may offer more practical and cost-effective solutions.
Platinum Resistance Thermometer:
A Platinum Resistance Thermometer (PRT), also known as a platinum resistance temperature detector (RTD), is a type of thermometer that utilizes the change in electrical resistance of platinum wire with temperature to measure temperature accurately. The Platinum Resistance Thermometer works on the principle that the resistance of a platinum wire changes in a predictable manner as the temperature changes. Platinum is chosen for its linear resistance-temperature relationship, high stability, and repeatability over a wide temperature range.
Construction:

The construction of a Platinum Resistance Thermometer (PRT) involves several key components and considerations to ensure accurate temperature measurement. The construction of a typical PRT is as follows:
- Platinum Wire: The heart of a PRT is a fine platinum wire that exhibits a predictable change in electrical resistance with temperature variations. Platinum is chosen for its linear resistance-temperature relationship, stability, and repeatability over a wide temperature range.
- Support Structure: The platinum wire is typically wound around a support structure made of a non-conductive material, such as ceramic or glass. This support structure provides mechanical stability and protection for the platinum wire.
- Lead Wires: Electrical lead wires are attached to the platinum wire to allow for connection to a measurement circuit. The lead wires should be made of a conductive material that does not introduce significant resistance or interference.
- Encapsulation: The platinum wire and support structure are often encapsulated in a protective sheath or housing. This encapsulation helps to shield the PRT from external factors such as moisture, contaminants, and mechanical damage.
- Calibration Markers: PRTs are calibrated at specific reference temperatures to establish the relationship between resistance and temperature. Calibration markers or reference points may be added to the PRT to aid in calibration and temperature measurement.
- Terminal Connection: The terminal connection point where the lead wires are connected to the external measurement circuit is usually located on the housing or sheath of the PRT. This connection point should be securely sealed to prevent moisture ingress and ensure reliable electrical contact.
- Measurement Circuit (External): PRTs are typically used in a Wheatstone bridge circuit configuration. A known current is passed through the platinum wire, and the voltage drop across the wire is measured. The resistance of the wire, and thus the temperature, can be calculated using the voltage and the known current.
Working:
The resistance of the platinum wire changes with temperature following the Callendar-Van Dusen equation or the ITS-90 (International Temperature Scale of 1990) standard. This change is typically very linear over a wide range of temperatures, providing excellent accuracy and stability.
Once calibrated, the PRT can be used to measure temperatures by measuring the resistance of the platinum wire and using the calibration coefficients to calculate the corresponding temperature. The temperature measurement can be displayed directly on a digital thermometer or transmitted to a data acquisition system for further processing.
Advantages of PTR:
Platinum Resistance Thermometers (PRTs) offer several advantages compared to other types of temperature sensors. Here are some of the key advantages:
- High Accuracy: PRTs provide highly accurate temperature measurements over a wide range of temperatures. Platinum has a linear resistance-temperature relationship, allowing for precise and reliable temperature readings.
- Stability: PRTs offer excellent long-term stability and repeatability. The resistance-temperature characteristics of platinum are well-defined and consistent, resulting in stable and reliable temperature measurements over time.
- Wide Temperature Range: PRTs can measure temperatures ranging from cryogenic temperatures to several hundred degrees Celsius or higher. They offer a wide temperature range of operation, making them suitable for various applications across different industries.
- Linear Response: The resistance of platinum in PRTs changes linearly with temperature variations, simplifying calibration and temperature compensation processes.
- Repeatability: PRTs provide repeatable temperature measurements, allowing for consistent results in laboratory experiments, industrial processes, and other applications.
- Low Drift: PRTs exhibit minimal drift over time, ensuring that temperature measurements remain accurate and reliable over extended periods.
- High Sensitivity: Platinum has a relatively high temperature coefficient of resistance (TCR), resulting in high sensitivity to temperature changes. This high sensitivity enables PRTs to detect small temperature variations accurately.
- Interchangeability: PRTs are highly interchangeable, meaning that different PRTs of the same type can be used interchangeably without significant calibration adjustments. This interchangeability simplifies instrument calibration and maintenance procedures.
- Low Self-Heating: PRTs generate minimal self-heating when subjected to an electrical current, reducing the impact of self-heating on temperature measurements.
- Compatibility with Standardization: PRTs are widely used as reference standards in laboratories and industries due to their high accuracy, stability, and compatibility with standardization efforts such as the International Temperature Scale of 1990 (ITS-90).
Disadvantages of PRT:
While Platinum Resistance Thermometers (PRTs) offer many advantages, they also have some disadvantages and limitations. Here are some of the main drawbacks of PRTs:
- Cost: PRTs can be relatively expensive compared to other types of temperature sensors. The cost of platinum, as well as the precision manufacturing required to produce accurate PRTs, contributes to their higher price.
- Fragility: PRTs can be fragile due to their fine platinum wire construction and delicate support structures. They may be more susceptible to mechanical damage, such as bending or breaking, compared to some other types of temperature sensors.
- Slow Response Time: PRTs generally have a slower response time compared to some other temperature sensors, such as thermocouples. The time required for the platinum wire to reach thermal equilibrium with the surrounding environment can result in slower temperature response times.
- Limited Temperature Range: While PRTs can measure temperatures over a wide range, they may not be suitable for extreme temperature conditions, such as those encountered in very high-temperature industrial processes or in cryogenic applications. Extreme temperatures can affect the performance and accuracy of PRTs.
- Susceptibility to Contamination: PRTs can be sensitive to contamination of the platinum wire, which can affect their accuracy and stability. Contaminants such as moisture, gases, or particulate matter can introduce errors and require thorough cleaning and maintenance procedures.
- Electrical Excitation Required: PRTs require an external electrical excitation source to measure temperature accurately. This requirement for electrical excitation can introduce additional complexity and potential sources of error in temperature measurement systems.
- Limited Flexibility: The physical construction and design of PRTs may limit their flexibility in certain applications. They may not be as adaptable to harsh environments or space-constrained installations compared to some other types of temperature sensors.
- Calibration Requirements: PRTs require periodic calibration to maintain accurate temperature measurements over time. Calibration procedures can be time-consuming and may require specialized equipment and expertise.
Despite these disadvantages, PRTs remain widely used in many industries and applications where high accuracy, stability, and repeatability are essential for precise temperature measurement. It’s important to consider the specific requirements of each application when selecting a temperature sensor and to weigh the advantages and disadvantages of different sensor types accordingly.
Thermocouple:
A thermocouple is a type of temperature sensor that consists of two different metal wires joined together at one end, called the junction. When there is a temperature gradient along the length of the thermocouple, it generates a voltage proportional to the temperature difference between the two ends. This phenomenon is known as the Seebeck effect.

Construction:
A thermocouple is a temperature sensor that operates based on the Seebeck effect, which describes the generation of a voltage when two dissimilar metals are joined together at a junction and there is a temperature gradient along the length of the metals.
- Metal Wires: Thermocouples consist of two different metal wires joined together at one end to form the sensing junction. The metals used in the wires determine the thermocouple type and its temperature range. Common metal combinations include chromel-alumel (Type K), iron-constantan (Type J), and copper-constantan (Type T), among others.
- Insulation: The metal wires are typically insulated from each other along their length to prevent electrical shorting. The insulation material is chosen to withstand the temperature and environmental conditions of the application.
- Protection Sheath: In many applications, the thermocouple wires are housed within a protective sheath made of stainless steel, ceramic, or other suitable materials. The sheath shields the thermocouple from mechanical damage, corrosion, and environmental factors.
- Connection Head: At the end opposite the sensing junction, the thermocouple wires are connected to a termination point, usually within a connection head. The connection head provides a secure enclosure for the wiring connections and allows for easy access for calibration and maintenance.
Working:
- Seebeck Effect: When there is a temperature gradient along the length of the two dissimilar metal wires forming the sensing junction, a voltage is generated. This voltage is proportional to the temperature difference between the sensing junction and the reference (cold) junction, usually located at or near the termination point.
- Measurement Circuit: The voltage generated by the thermocouple is measured using a voltmeter or a temperature measurement device. The voltage is typically very small, so the measurement circuit needs to be sensitive to detect it accurately. Generally wheatstone’s bridge is used.
- Cold Junction Compensation: Accurate temperature measurement with a thermocouple requires compensation for the temperature of the reference (cold) junction. Specialized circuits or techniques are used to measure the temperature at the reference junction and compensate for its effect on the thermocouple output.
- Temperature Calculation: Once the voltage generated by the thermocouple is measured and compensated for the reference junction temperature, it is converted into a temperature reading using calibration tables or equations specific to the thermocouple type and temperature range.
Overall, thermocouples are widely used temperature sensors in various industries and applications due to their wide temperature range, fast response time, durability, and simplicity of construction.
Types of Thermocouples:
Type of Thermocouple | Wires Used | Temperature Range in oC |
B | Platinum (6% Rhodium) and Platinum (30% Rhodium) | 1370 to 1700 |
E | Chromel and Constantan | 0 to 870 |
J | Iron and Constantan | 0 to 760 |
K | Chromel and Alumel | 95 to 1260 |
N | Nicrosil and Nisil | 650 to 1260 |
R | Platinum (13% Rhodium) and Platinum | 870 to 1450 |
S | Platinum (10% Rhodium) and Platinum | 980 to 1450 |
T | Copper and Constantan | -200 to 370 |
Advantages of Thermocouple:
Thermocouples offer several advantages that make them widely used for temperature measurement in various industries and applications.
- Wide Temperature Range: Thermocouples can measure temperatures ranging from cryogenic temperatures to extremely high temperatures (up to around 2300°C or 4172°F), depending on the type of thermocouple and the materials used. This wide temperature range makes thermocouples suitable for a broad range of applications across different industries.
- Fast Response Time: Thermocouples have a fast response time, allowing for rapid temperature measurement and monitoring. This makes them well-suited for applications where quick temperature changes need to be detected or controlled.
- Robustness and Durability: Thermocouples are relatively robust and durable temperature sensors. They can withstand harsh environments, mechanical vibrations, and high electromagnetic interference, making them suitable for use in industrial environments and challenging conditions.
- Simple Construction: Thermocouples consist of only two wires joined together at one end, making them simple in construction and easy to install. Their simplicity makes them cost-effective and versatile for various applications.
- Wide Variety of Types and Materials: Thermocouples are available in a wide variety of types and materials, each offering different temperature ranges, accuracies, and characteristics. Common types include Type K, Type J, Type T, and Type E thermocouples, each suitable for specific temperature ranges and environments.
- Compatibility with Many Environments: Thermocouples are compatible with many different environments and can be used in various gases, liquids, and solids. They are widely used in industrial processes, HVAC systems, automotive applications, and scientific research.
- No External Power Required: Thermocouples generate their own voltage signal when subjected to a temperature gradient, eliminating the need for external power sources. This makes them suitable for remote or portable applications where power may be limited or unavailable.
- Interchangeability: Thermocouples are highly interchangeable, meaning that different thermocouples of the same type can be used interchangeably without significant calibration adjustments. This interchangeability simplifies instrument calibration and maintenance procedures.
- Cost-Effective: Thermocouples are generally more cost-effective compared to some other types of temperature sensors, such as resistance temperature detectors (RTDs) and infrared thermometers. Their simple construction, durability, and versatility contribute to their cost-effectiveness.
Overall, thermocouples offer many advantages, including wide temperature range, fast response time, robustness, simplicity, compatibility with various environments, and cost-effectiveness, making them one of the most commonly used temperature sensors in numerous industrial, commercial, and scientific applications.
Disadvantages of Thermocouple:
While thermocouples offer many advantages, they also have some disadvantages and limitations. Here are some of the key disadvantages of thermocouples:
- Non-Linear Output: The voltage output of a thermocouple is non-linear with temperature, especially over wide temperature ranges. This non-linearity can introduce errors in temperature measurements, requiring compensation and correction techniques to achieve accurate readings.
- Cold Junction Compensation: Accurate temperature measurement with thermocouples requires compensation for the temperature of the reference junction (cold junction). Specialized equipment or compensation techniques are used to account for temperature variations at the cold junction, adding complexity to temperature measurement systems.
- Limited Accuracy: While thermocouples offer good accuracy for many industrial applications, they may not be as accurate as some other temperature sensors, such as resistance temperature detectors (RTDs), especially at lower temperatures. The accuracy of thermocouples can be affected by factors such as wire quality, calibration, and environmental conditions.
- Sensitivity to Electrical Noise: Thermocouples are susceptible to electrical noise and interference, which can affect the accuracy and stability of temperature measurements. Proper shielding and grounding techniques are required to minimize the impact of electrical noise on thermocouple signals.
- Limited Resolution: Thermocouples have limited resolution compared to some other temperature sensors, such as RTDs and thermistors. The resolution of a thermocouple is determined by the sensitivity of the thermocouple and the accuracy of the measurement system.
- Limited Temperature Range for Some Types: While thermocouples offer a wide temperature range overall, some specific types of thermocouples have limited temperature ranges. For example, Type T thermocouples have a relatively narrow temperature range compared to other types, making them unsuitable for high-temperature applications.
- Susceptibility to Corrosion and Contamination: Certain environments can cause corrosion or contamination of thermocouple materials, affecting their accuracy and reliability over time. Protective sheaths or coatings may be required to protect thermocouples in corrosive or contaminating environments.
- Heterogeneity and Stability Issues: Thermocouples made from different materials may exhibit heterogeneity in their characteristics, leading to variations in temperature measurements. Additionally, thermocouples may suffer from stability issues over time, resulting in drift and changes in calibration.
Despite these disadvantages, thermocouples remain widely used for temperature measurement in various industries and applications due to their versatility, ruggedness, wide temperature range, and suitability for harsh environments. It’s important to consider the specific requirements of each application and weigh the advantages and disadvantages of different temperature sensors accordingly.
Pyrometers:
A pyrometer is a device used to measure the temperature of objects or surfaces without making physical contact. Pyrometers work based on the principle of measuring the thermal radiation emitted by an object, which is related to its temperature according to the laws of blackbody radiation. One of the primary advantages of pyrometers is that they can measure the temperature of objects without physical contact. This is particularly useful for measuring the temperature of objects that are moving, inaccessible, or hazardous to touch. Pyrometers are used in a wide range of industrial, scientific, and commercial applications, including metal processing, glass manufacturing, ceramics, automotive, aerospace, and research laboratories. They are particularly useful for monitoring and controlling temperatures in high-temperature processes and environments

- Principle of Operation: Pyrometers measure the intensity of thermal radiation emitted by an object, usually within the infrared spectrum. The intensity of thermal radiation emitted by an object is directly related to its temperature, according to the Stefan-Boltzmann law and Planck’s law of blackbody radiation.
- Optical System: Pyrometers typically employ an optical system to focus the thermal radiation emitted by the object onto a detector. The optical system may include lenses, mirrors, or fibre optics to collect and direct the radiation to the detector.
- Detector: The detector in a pyrometer converts the incoming thermal radiation into an electrical signal. Different types of detectors may be used, including thermopiles, bolometers, and photodiodes, depending on the specific application and temperature range.
- Accuracy and Calibration: The accuracy of temperature measurements with pyrometers depends on various factors, including the calibration of the instrument, the stability of the detector, and the emissivity of the object being measured. Calibration standards and procedures are used to ensure accurate temperature measurements.
Advantages of Pyrometer:
Pyrometers offer several advantages in temperature measurement, particularly in situations where non-contact measurement and high-temperature sensing are required. Here are some key advantages of pyrometers:
- Non-contact Measurement: Pyrometers enable temperature measurement without physical contact with the object being measured. This feature is especially valuable for measuring the temperature of moving objects, fragile materials, or objects at high temperatures where contact measurement may be impractical or impossible.
- Wide Temperature Range: Pyrometers can measure temperatures ranging from low (e.g., room temperature) to extremely high temperatures (e.g., thousands of degrees Celsius). This wide temperature range makes them suitable for various industrial, scientific, and commercial applications, including metal processing, glass manufacturing, ceramics, and automotive.
- Fast Response Time: Pyrometers offer fast response times, allowing for rapid temperature measurements. This makes them ideal for applications where temperature changes need to be monitored or controlled quickly, such as industrial processes, combustion monitoring, and materials processing.
- Remote Sensing: Pyrometers can measure temperature from a distance, making them suitable for measuring objects that are difficult to access or located in hazardous environments. They are commonly used in industrial furnaces, kilns, and reactors where direct contact measurement is not feasible.
- Versatility: Pyrometers are versatile instruments that can be used in various environments and applications. They are available in different configurations, including portable handheld units, fixed-mount units, and online monitoring systems, to meet specific measurement requirements.
- Accuracy and Precision: Modern pyrometers offer high levels of accuracy and precision in temperature measurement. They employ advanced optics, detectors, and signal processing techniques to ensure accurate and reliable temperature readings across a wide range of temperatures and operating conditions.
- Durability and Reliability: Pyrometers are designed to withstand harsh industrial environments, including high temperatures, dust, humidity, and vibration. They are built with rugged enclosures, durable optics, and robust electronics to ensure long-term reliability and performance in demanding applications.
- Real-time Monitoring and Control: Pyrometers can be integrated into automated systems for real-time temperature monitoring and control. They provide valuable data for process optimization, quality control, and predictive maintenance in manufacturing and industrial processes.
- Safety: Pyrometers contribute to improved safety in industrial environments by enabling temperature measurement from a safe distance, reducing the risk of operator exposure to hazardous conditions or hot surfaces.
Thus, pyrometers offer numerous advantages in temperature measurement, including non-contact measurement, wide temperature range, fast response time, versatility, accuracy, durability, and safety. These features make them indispensable tools in a wide range of industries and applications where precise and reliable temperature measurement is essential.
Disadvantages of Pyrometers:
While pyrometers offer many advantages in temperature measurement, they also have some limitations and disadvantages.
- Emissivity Variations: Pyrometers rely on the assumption of uniform emissivity, which refers to the ability of a surface to emit thermal radiation. However, the emissivity of real-world surfaces can vary based on factors such as surface finish, material composition, and surface condition. Variations in emissivity can lead to measurement errors and inaccuracies.
- Limited Accuracy at Low Temperatures: Pyrometers may have limited accuracy at low temperatures, especially below 100°C (212°F). At lower temperatures, the emitted thermal radiation is relatively weak, making it challenging to distinguish the signal from background noise accurately.
- Distance-to-Spot Ratio: Pyrometers have a specified distance-to-spot ratio, which determines the size of the measurement area at a given distance. In applications where precise targeting is required, limitations in the distance-to-spot ratio can affect the accuracy of temperature measurements.
- Reflection and Interference: Reflections from nearby surfaces and interference from ambient light sources can affect the accuracy of pyrometer measurements. Reflected radiation can lead to errors in temperature readings, particularly in environments with shiny or reflective surfaces.
- Cost: High-quality pyrometers with advanced features and capabilities can be relatively expensive compared to other temperature measurement devices, such as thermocouples and thermistors. The cost of calibration, maintenance, and training may also contribute to the overall expense of implementing pyrometry systems.
- Calibration and Maintenance: Pyrometers require regular calibration to ensure accurate and reliable temperature measurements. Calibration procedures can be complex and time-consuming, requiring specialized equipment and trained personnel. Additionally, pyrometers may require periodic maintenance to ensure proper functionality and performance.
- Limited Temperature Range for Some Types: While pyrometers can measure a wide range of temperatures, some specific types may have limited temperature ranges. Certain pyrometer technologies may not be suitable for extremely high-temperature applications or very low-temperature measurements.
- Response Time: While pyrometers generally offer fast response times, the response time can vary depending on the type of pyrometer, measurement distance, and environmental conditions. In some applications where rapid temperature changes occur, limitations in response time may impact the accuracy of temperature measurements.
- Complexity of Operation: Some types of pyrometers, particularly those with advanced features and capabilities, may be complex to operate and require specialized training and expertise. Users need to understand the principles of operation, calibration procedures, and potential sources of error to obtain accurate temperature measurements.
Despite these disadvantages, pyrometers remain valuable tools for temperature measurement in various industries and applications where non-contact measurement, high-temperature sensing, and remote monitoring are required. It’s essential to consider the specific requirements of each application and weigh the advantages and disadvantages of pyrometers accordingly.
Thermistors:
A thermistor thermometer is a type of thermometer that utilizes a thermistor as its temperature sensing element. Thermistors are temperature-sensitive resistors made from semiconductor materials whose electrical resistance changes significantly with temperature variations. Thermistor thermometers find applications in various industries and applications, including HVAC (heating, ventilation, and air conditioning) systems, automotive, medical devices, food processing, and environmental monitoring. They are particularly useful for applications requiring accurate and reliable temperature measurements over a relatively narrow temperature range.
Construction:

The construction of a thermistor thermometer involves the integration of a thermistor, which is a temperature-sensitive resistor made from semiconductor materials, into a measurement circuit.
- Principle of Operation: Thermistors operate based on the principle of the change in electrical resistance with temperature variations. They exhibit a negative temperature coefficient (NTC) or positive temperature coefficient (PTC) depending on the type of thermistor. NTC thermistors have decreasing resistance with increasing temperature, while PTC thermistors have increasing resistance with increasing temperature.
- Thermistor: The core component of a thermistor thermometer is the thermistor itself. Thermistors are typically made from semiconductor materials such as metal oxides (e.g., nickel, manganese, cobalt), which exhibit a predictable change in resistance with temperature variations. The choice of thermistor type (e.g., NTC or PTC) depends on the specific application requirements.
- Housing: The thermistor is housed within a protective casing or probe to shield it from environmental factors and physical damage. The housing material is selected to withstand the operating conditions of the application, including temperature, humidity, and chemical exposure.
- Wiring: The thermistor is connected to the measurement circuit using electrical wiring. The wiring should be of sufficient quality and gauge to minimize resistance and signal loss.
- Measurement Circuit: The measurement circuit comprises components such as resistors, capacitors, operational amplifiers, and possibly microcontrollers or integrated circuits (ICs) for signal processing and data display. The circuit is designed to measure the resistance of the thermistor accurately and convert it into a temperature reading.
- Voltage Source: A voltage source is typically provided to supply power to the measurement circuit and thermistor. The voltage source may be a battery, power supply, or integrated power management circuit, depending on the application requirements.
- Calibration Components: Calibration components, such as precision resistors and trim pots, may be included in the measurement circuit to calibrate the thermometer and ensure accurate temperature readings. Calibration is essential to account for variations in thermistor characteristics and circuit performance.
- Display and Output: The temperature reading obtained from the measurement circuit is displayed to the user through a digital display (e.g., LCD or LED) or analog gauge. Some thermistor thermometers may also include output options such as analog voltage output, serial communication (e.g., UART), or digital protocols (e.g., I2C, SPI) for interfacing with external devices or data logging systems.
- Enclosure: The entire thermometer assembly, including the measurement circuit, display, and wiring, may be enclosed within a protective housing or casing. The enclosure provides physical protection, electrical insulation, and mounting options for the thermometer.
- User Interface: Depending on the thermometer’s design and intended use, it may include user interface elements such as buttons, switches, or touchscreens for setting parameters, adjusting settings, or accessing additional features.
The construction of a thermistor thermometer can vary depending on factors such as the thermometer’s intended application, accuracy requirements, environmental conditions, and cost considerations. However, the basic principles outlined above form the foundation of most thermistor thermometer designs.
Advantages of Thermistor Thermometers:
Thermistor thermometers offer several advantages in temperature measurement, particularly in applications where high sensitivity, accuracy, and precision are required. Here are some key advantages of thermistor thermometers:
- High Sensitivity: Thermistors exhibit high sensitivity to temperature changes, making them capable of detecting even small variations in temperature. This high sensitivity allows for precise temperature measurements in a wide range of applications.
- Wide Temperature Range: Thermistor thermometers can measure temperatures across a broad range, from cryogenic temperatures to elevated temperatures. Different types of thermistors, such as negative temperature coefficient (NTC) and positive temperature coefficient (PTC) thermistors, offer temperature measurement capabilities over different ranges, providing versatility in various applications.
- Linearity: Thermistors often exhibit a linear relationship between resistance and temperature over a specific temperature range, simplifying calibration and temperature measurement calculations. This linearity enhances accuracy and precision in temperature measurement compared to some other temperature sensors.
- Fast Response Time: Thermistors have a fast response time, allowing for rapid temperature measurement and monitoring. This feature is particularly useful in applications where quick temperature changes need to be detected or controlled.
- Small Size: Thermistors are compact and lightweight, making them suitable for integration into small, space-constrained devices and systems. Their small size allows for easy installation and integration into various electronic devices and equipment.
- Low Cost: Thermistors are relatively inexpensive compared to some other temperature sensors, such as resistance temperature detectors (RTDs) and thermocouples. Their low cost makes them an economical choice for temperature measurement in many applications.
- Stability and Long-Term Reliability: Thermistors exhibit stable and consistent performance over time, with minimal drift in resistance and temperature measurement accuracy. This stability ensures long-term reliability and repeatability in temperature measurements, reducing the need for frequent calibration and maintenance.
- Low Power Consumption: Thermistors have low power consumption, making them energy-efficient and suitable for battery-powered applications and portable devices. Their low power requirements contribute to extended battery life and reduced operating costs.
- Ease of Interfacing: Thermistors can be easily interfaced with electronic circuits and microcontrollers for temperature measurement and control. Their simple electrical characteristics and predictable behaviour simplify circuit design and integration into electronic systems.
- Compatibility with Semiconductor Processes: Thermistors are semiconductor devices and are compatible with semiconductor manufacturing processes, allowing for cost-effective production and customization for specific application requirements.
Thus, thermistor thermometers offer several advantages, including high sensitivity, wide temperature range, linearity, fast response time, small size, low cost, stability, low power consumption, ease of interfacing, and compatibility with semiconductor processes. These features make them valuable temperature sensors in various industrial, commercial, and consumer applications where accurate and reliable temperature measurement is essential.
Disadvantages of Thermistor Thermometer:
Thermistors, while offering many advantages in temperature measurement, also have some limitations and disadvantages. Here are some of the key disadvantages of thermistors:
- Non-linearity: One significant drawback of thermistors is their non-linear resistance-temperature relationship. Unlike some other temperature sensors like resistance temperature detectors (RTDs), the resistance of a thermistor does not change linearly with temperature. This non-linearity can complicate calibration and temperature measurement calculations, requiring curve fitting or lookup tables for accurate temperature readings.
- Limited Temperature Range: Thermistors have a limited temperature range compared to some other temperature sensors, such as thermocouples. While they are suitable for many applications, thermistors may not be appropriate for extremely high-temperature measurements or cryogenic temperatures.
- Self-Heating: Thermistors exhibit self-heating when current passes through them to measure temperature. This self-heating effect can lead to inaccuracies in temperature measurements, especially at low currents or when high precision is required. Careful consideration and compensation techniques may be necessary to mitigate the impact of self-heating on temperature readings.
- Stability and Drift: Thermistors may exhibit stability issues and long-term drift in resistance over time. Factors such as aging, environmental conditions (e.g., temperature, humidity), and mechanical stress can contribute to changes in thermistor characteristics and performance. Regular calibration and maintenance may be required to ensure consistent and reliable temperature measurements.
- Limited Interchangeability: Thermistors are not as interchangeable as some other temperature sensors, such as thermocouples and RTDs. Each thermistor has unique characteristics, including resistance-temperature curves and tolerances, which can vary between different thermistors even of the same type and model. This lack of interchangeability can complicate replacement and calibration processes.
- Sensitivity to Overvoltage and Transients: Thermistors are sensitive to overvoltage and transient voltage spikes, which can damage or degrade their performance. Proper voltage protection measures, such as transient voltage suppressors (TVS diodes) and voltage regulators, may be necessary to safeguard thermistors from electrical overstress.
- Limited Availability of Standardized Models: Unlike some other temperature sensors, such as thermocouples and RTDs, thermistors may have limited availability of standardized models with well-defined specifications and calibration standards. This can make it challenging to select and integrate thermistors into temperature measurement systems, especially in critical or regulated applications.
Despite these disadvantages, thermistors remain widely used for temperature measurement in various industrial, commercial, and consumer applications due to their high sensitivity, low cost, compact size, and ease of integration. It’s important to consider the specific requirements and limitations of thermistors when selecting temperature sensors for different applications.
Liquid Crystal Thermometer:
Liquid crystal thermometers, also known as liquid crystal temperature strips or liquid crystal thermochromic devices, are temperature-sensitive devices that use liquid crystal materials to display temperature information. Here’s an overview of liquid crystal thermometers:
Construction:
- Liquid Crystal Material: The core component of a liquid crystal thermometer is the liquid crystal material itself. Liquid crystals are organic compounds that exhibit changes in color or opacity in response to changes in temperature. These changes occur due to alterations in the molecular arrangement of the liquid crystal material as temperature changes.
- Substrate: The liquid crystal material is typically encapsulated within a thin, transparent plastic or polyester substrate. This substrate serves as a protective layer and provides support for the liquid crystal material.
- Adhesive Backing: Many liquid crystal thermometers feature an adhesive backing on one side of the substrate, allowing them to be affixed to various surfaces, such as containers, windows, or equipment.
Working Principle:
- Temperature Sensitivity: Liquid crystal thermometers utilize the temperature sensitivity of liquid crystal materials. As the temperature changes, the liquid crystal molecules reorient themselves, causing changes in the material’s optical properties, such as color or opacity.
- Colour Change: Liquid crystal thermometers typically feature a color scale printed on the substrate adjacent to the liquid crystal material. As the temperature changes, the liquid crystal material changes colour according to the temperature scale, providing a visual indication of the current temperature.
- Visual Observation: Users can visually observe the colour changes in the liquid crystal material to determine the approximate temperature. The colours may indicate temperature ranges or specific temperature values, depending on the design of the thermometer.
Advantages of Liquid Crystal Thermometers:
- Non-Invasive Measurement: Liquid crystal thermometers offer non-invasive temperature measurement, requiring no direct contact with the object or surface being measured. This feature is particularly useful for applications where contact measurement methods are impractical or undesirable.
- Quick Response Time: Liquid crystal thermometers have a fast response time, allowing users to quickly assess temperature changes. The colour changes in the liquid crystal material occur almost instantly in response to temperature variations.
- Compact and Portable: Liquid crystal thermometers are lightweight, compact, and portable, making them easy to transport and use in various settings. They are particularly convenient for field measurements or mobile applications.
- Low Cost: Liquid crystal thermometers are generally inexpensive compared to some other temperature measurement devices, such as digital thermometers or infrared thermometers. They offer a cost-effective solution for temperature monitoring and measurement.
- Visual Readout: Liquid crystal thermometers provide a visual readout of temperature information, eliminating the need for power sources or electronic displays. This simplicity makes them easy to use and understand, even for individuals without technical expertise.
Disadvantages of Liquid Crystal Thermometers:
- Limited Precision: Liquid crystal thermometers may provide only approximate temperature measurements and are typically less precise than digital thermometers or thermocouples.
- Temperature Range: The temperature range of liquid crystal thermometers may be limited compared to other temperature measurement devices. They may not be suitable for extreme temperature conditions or high-precision applications.
- Subject to Environmental Factors: Liquid crystal thermometers can be affected by environmental factors such as humidity, sunlight, and ambient temperature variations, which may impact their accuracy and performance.
Applications:
Liquid crystal thermometers are commonly used in various applications, including home temperature monitoring, medical diagnostics, aquariums, and educational settings. They provide a simple and convenient method for assessing temperature changes in a wide range of environments
Conclusion:
Temperature is measured using various types of temperature sensors and instruments, each with its own principles of operation, advantages, and limitations. Each temperature measurement method has its own advantages, limitations, and application-specific considerations. The choice of temperature sensor or instrument depends on factors such as the temperature range, accuracy requirements, response time, environmental conditions, and specific application needs.